在线电导率检测仪的电极表面状态直接影响测量精度,长期使用后、生物膜及矿物质结晶会导致电极常数偏离初始值 10% 以上,使测量误差从 ±1% 增至 ±5%。科学规范的清洗规程可去除附着污染物,恢复电极响应性能,确保在饮用水、工业循环水等场景的监测数据可靠。 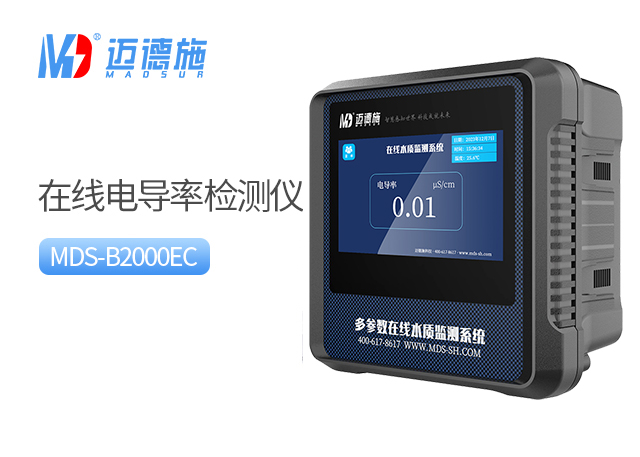
清洗周期的动态设定需结合应用场景。在市政自来水厂(浊度<1NTU),建议每 2 周清洗一次;工业循环水系统(浊度 5-20NTU)需缩短至每周一次;而在污水处理厂出口(浊度>50NTU),应每 3 天清洗一次。当仪器显示 “电极污染” 告警(部分型号具备)或测量值漂移超过 5% 时,需立即启动应急清洗。判断污染类型可辅助选择清洗方式:电极表面出现白色结晶(多为碳酸钙),优先采用酸洗;呈现褐色或黑色附着物(生物膜或铁锰氧化物),需用氧化剂或酶制剂处理。 物理清洗的基础操作适用于轻度污染。首先关闭检测仪的进样阀,将电极从管道中取出(若为浸入式),用软毛刷(尼龙材质,毛长 5mm)蘸取去离子水轻轻刷洗电极表面,重点清除附着的泥沙与松散生物膜,避免使用金属刷或硬塑料刷损伤铂黑镀层。对于流通式安装的电极,可开启反冲洗装置:用 0.2MPa 的去离子水反向冲洗 30 秒,利用水流冲击力清除管道内的沉积物,反冲洗频率可设置为正常测量的 1/10(如每测量 10 次反冲 1 次)。超声波清洗适用于顽固颗粒物:将电极放入专用清洗槽(功率 50W,频率 40kHz),用去离子水淹没电极 2cm,清洗 5 分钟后取出,这种方式可使铂黑电极的清洁度提升 40%,但需注意每次清洗时间不超过 10 分钟,防止镀层脱落。 化学清洗的分级处理需针对性实施。针对矿物质结垢,采用 10% 柠檬酸溶液浸泡:将电极完全浸入溶液,静置 15 分钟(温度 25℃),期间每 5 分钟晃动一次容器,确保酸液充分接触电极表面。柠檬酸可螯合钙、镁离子,溶解率达 90% 以上,浸泡后用去离子水冲洗至中性(pH 6-7),避免残留酸液腐蚀电极基体。生物膜污染需用 5% 次氯酸钠溶液处理:浸泡 10 分钟后,用软刷轻擦电极,次氯酸的氧化作用可分解生物膜的有机成分,杀菌率达 99%,处理后必须冲洗至无氯味(余氯<0.1mg/L),防止对后续测量产生干扰。含油污水监测后的电极,需先用石油醚浸泡 5 分钟去除油膜,再用去离子水冲洗,避免油分封闭电极表面影响离子传导。 特殊污染的进阶处理需专业操作。铁锰氧化物污染(常见于地下水监测)可采用 1% 盐酸羟胺溶液(还原性清洗剂),60℃水浴加热条件下浸泡 20 分钟,还原反应能使黑色附着物溶解率提升至 85%。对于含硫化物的工业废水场景,电极表面可能形成硫化银沉淀,需用 5% 硝酸银溶液浸泡 10 分钟,通过置换反应生成可溶银盐,再用硫代硫酸钠溶液中和残留银离子。化学清洗后必须进行活化处理:将电极浸入 0.01mol/L 氯化钾溶液中静置 30 分钟,使电极表面形成稳定的双电层,活化后的电极初始电位应在 - 150mV 至 - 250mV(vs Ag/AgCl)。 清洗后的性能验证不可或缺。用 0.1mol/L 氯化钾标准溶液(25℃时电导率 1413μS/cm)进行校准,测量值与标准值的相对误差应≤2%,否则需重复清洗步骤。检查电极响应速度:测量 100μS/cm 和 1000μS/cm 的标准液,达到稳定值的时间应≤30 秒,较清洗前缩短 50% 以上说明清洗有效。对于双电极体系,需分别测量两个电极的常数偏差,差值应<0.01cm⁻¹,确保对称性良好。验证合格后,按安装规程将电极复位,启动正常测量程序,前 3 次测量数据需剔除,待读数稳定后记录。 清洗操作的安全规范需严格遵守。化学试剂需佩戴防护装备:接触酸液时戴耐酸碱手套(如丁腈材质)和护目镜,操作次氯酸时需在通风处进行,避免氯气吸入。清洗废液需分类处理:酸性废液用氢氧化钠中和至 pH 6-9 后排放;含重金属的清洗液(如硝酸银废液)需单独收集,交专业机构处置。清洗工具需专用:酸洗与碱洗的容器、刷子必须分开存放(标注明显标识),避免交叉污染。每次清洗需记录:清洗时间、污染类型、所用试剂、验证结果及操作人员,形成可追溯的维护档案,档案保存期不少于 2 年。 通过这套分级清洗规程,在线电导率检测仪的电极性能可恢复至初始状态的 95% 以上,有效延长电极使用寿命(从 6 个月延长至 1 年),降低运维成本。实际应用中需根据水体特性动态调整清洗策略,例如高硬度水体增加酸洗频率,生物活性高的水体强化杀菌处理,实现 “按需清洗、精准维护” 的管理目标。
|